The double roller granulator is a dry granulation process which uses pressure to agglomerate solid materials. The material is extruded by two counter rotating rollers, which are driven by eccentric sleeve or hydraulic system. When extruding a solid material, the air between the powder particles is first removed, and then the particles are rearranged to eliminate the voids between the materials. When the brittle material is extruded, some particles are crushed and the fine powder fills the space between the particles.
The work of the double roller granulator mainly includes two parts: one is extrusion, the other is granulation.
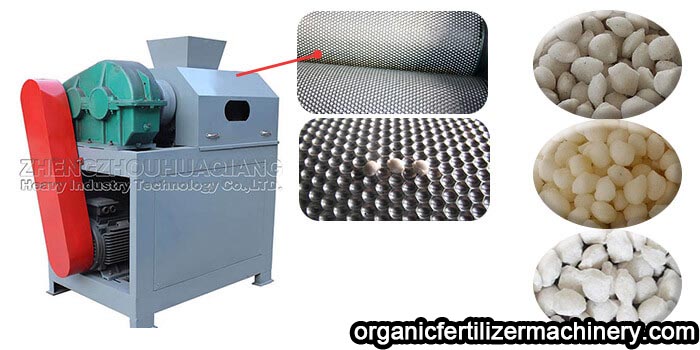
Extrusion: the dry material is in the shape of cake under the double roll extrusion of the double roller granulator. At this time, the density of the material is very high and the space between molecules is very small. Dry materials in the late storage of finished products, not easy to enter the air for moisture. In this process, the principle of intermolecular force in physics is also used to combine the extruded molecules into molecules with appropriate space density.
Granulation: crushing the pressed cake like material into many small particles by roller extruder granulator to achieve the purpose of granulation.
After strict extrusion granulation, the utilization rate of raw materials of the double roller granulator can reach more than 85%. Since there is no discharge of three wastes after repeated treatment, it supports environmental protection.
Compared with other granulators, the fertilizer granulation machine has more characteristics. The material is medium carbon steel plate with high hardness, high strength and channel steel welding. Strict quality control and process requirements are adopted. Lifting holes are set at four corners of the frame for loading, unloading and transportation.