The double roller granulator is driven by the motor belt and pulley, which is transmitted to the driving shaft through the reducer, and synchronized with the passive shaft through the split gear, working in opposite direction. The materials are added from the feeding hopper, extruded by rollers, demoulded and pelletized, and transported to the crushing Screen Studio through a pair of chains. The finished products (balls) are screened and separated, and then the returned materials are mixed with the new materials, and then granulated. With the continuous rotation of the motor and the continuous entry of materials, mass production can be realized.
Maintenance operation of double roller granulator
Sometimes there are grinding wheels on the frame of the double roller granulator. When there are pits or grooves on the roller surface, the roller surface can be ground and repaired on the machine without removing the roller surface, or it can be repaired directly on the roller surface, which requires the installation of surfacing device on the granulator.
When adjusting the double roller granulator, it is necessary to keep the two rollers parallel to each other to prevent skew.
When the movable roller is installed on the rocker arm or has a hydraulic compensation device, the axis of the two rollers will be parallel automatically when the moving roller moves.
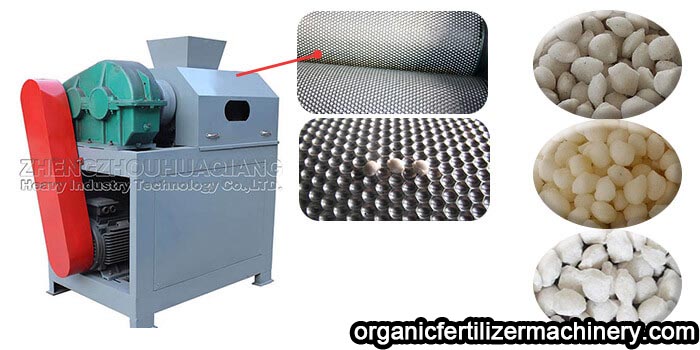
Matters needing attention on the double roller granulator
1. The fertilizer granulation machine should be started under no-load condition. It is forbidden to open with material.
2. The fertilizer granulation machine is forbidden to enter the material with iron to avoid breaking the roller shaft.
3. Before starting the machine, the gear should be smeared with yellow dry oil.
4. Apply yellow oil to the chain and sprocket every 7 days.
5. The bearing pedestal shall be filled or replaced with new yellow oil every three months.
6. The gear oil must be added once before the reducer is used in production. The gear oil should be changed every four months.