The double roller granulator is rolled and crushed into granules. At present, there are more than 20 kinds of materials successfully used in extrusion granulation: ammonium nitrate, urea, ammonium chloride, calcium nitrate, potassium chloride, potassium sulfate, etc. In addition, the extrusion granulation process can flexibly change the product formula in a very short time. A set of device can produce more than 30 kinds of products.
The design of the double roller granulator is very reasonable, practical and energy consumption is very low. It can be continuously produced at room temperature without drying. The ball and socket on the roller skin can be made according to the size and shape required by customers. At present, we have made spherical, pillow shaped, semicircular, bar shaped, pill shaped, walnut shaped, flat ball, square shaped, etc. New energy saving products are now used in compound fertilizer and organic fertilizer industry.
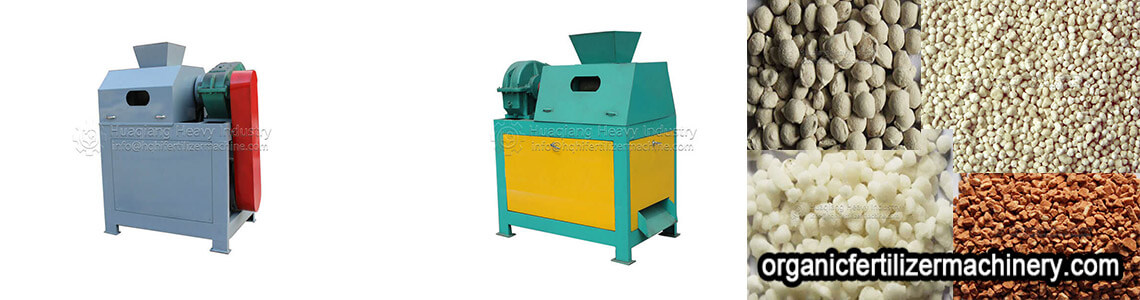
The working principle of the double roller granulator is very simple. There are four functions in total
1. In order to ensure that the fertilizer granulation machine can achieve continuous feeding during extrusion granulation, screw conveyor and vibration conveyor are generally used;
2. Then there is the forced feeding system, which is to control the feeding speed. As if the feeding speed is uniform, it can increase the feeding amount and increase the output. Its biggest function is to pre degass and apply pressure in advance, so as to make the product quality higher;
3. Double shaft output is adopted for roll extrusion, which can effectively improve the speed of transportation, protect the bearing capacity of the main shaft, reduce damage and improve the transmission effect. It can make the hydraulic cylinder have stable pressure and make the floating roller heel run smoothly.
4. Granulation: the material sent through the conveyor driven by the motor is crushed by the chopping system, and then the powdery material is evenly added into the binding plate for shaking, and then enters the roller mouth after forced degassing and pre pressing. According to the requirements of the particle specifications, with the rotation of the roller, the molding is gradually achieved. Then the automatic demoulding process is completed.